新能源汽车的市场,日趋火爆。核心动力源锂电池,自然对能量密度和综合性能提出更高要求。此外电池产品结构和配方不断升级换代,电芯对电解液的吸收自然是渴望猛吸。
坦白讲,锂电池电解液作用就是正负极之间导通离子,担当充放电的介质。可面对锂离子电池容量不断提高,电池尺寸持续增加的现状,如何让电解液充分而均匀的浸润到锂电池内部,成为疯狂的命题。
锂电池注液可分两步:1)注液 只需几秒钟将电解液注入电池内部 2)浸润 将注入的电解液吸收到电芯,这个非常耗时,需要注液和浸润反复进行,同时还必须是干燥环境中,这样极大增加锂离子电池生产成本。
电解液通过定量泵注入密封夹具内,将带密封圈的密封夹具与电池紧密联系在一起,然后空压机对电池进行抽真空,其次用氮气加压至0.2-1.0Mpa ,保压10-60分钟再放气到常压,然后是长时间静置(24-36h),从而让电解液与电池正负材料和隔膜充分浸润。
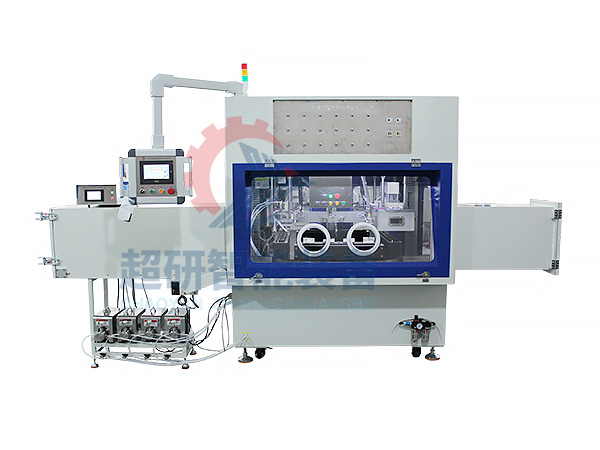
全自动注液机将电解液注入装配好的电池后,还自动称重来控制电解液注入量,后续再进行补液。
若电解液注入量过大,电池会发热甚至失效。若注入量过小,电池的循环性又会影响。同时电解液在电芯内部“均匀”的浸润,需要高真空度。电芯封口前,多次抽真空可提升均匀性。
事实上,重力对电解液浸润的影响微乎其微,真正影响比较大的是真空度。在真空环境注液能够将电解液的浸润时间降低50%,电芯吸收的电解液提高10%。因此增大正负压强差,改善注液温度等措施,都能提升注液效率。
注液设备目前的技术难点,主要体现在两方面:一是注液的精度控制,其直接影响电池使用性能;二是设备防腐蚀性,由于电解液有强腐蚀性,注液设备配件的材质必须具有较高要求。
超研智能多年注液机领域制作经验保证注液环境真空度,配置4大静置腔,可保证电池电解液吸收效果,提高生产效能,对比市场内注液机显著提高注液效果。